- Policy
- Targets and Promotion Plan
- Structure
- Distribution of Safety and Health Information and Occupational Accident Reports
- Employee Participation
- Risk Management
- Occupational Safety and Health Management Systems
- Training Programs
- Safety Award
- Data
Policy
Under the policies stating that thorough compliance, safety, and the environment are the foundation of our corporate activities and our basic principle is that safety is the absolute top priority, the Oji Group stipulates occupational safety and health in the Oji Group Corporate Code of Conduct and the Oji Group Behavior Standard.
We protect the safety and health of workers in workplaces by ensuring that every single employee understands these rules and standards regarding occupational safety and health, practices them and complies with them. At the same time, we work to create a comfortable workplace environment and establish a better workplace safety climate so that all of the workers within the Oji Group can work safely and with a feeling of security.
Relevant section of the Oji Group Corporate Code of Conduct
2. Developing a Rewarding Work Environment with Consideration for Safety and Health
We will develop a comfortable work environment which enhances the abilities of all employees and gives consideration to workstyles that respect diversity and individuality, and to safety and health.
Relevant sections of the Oji Group Behavior Standard
17. Ensuring Safety and Health in the Workplace
With "safety as the top priority," we will ensure safety and health in the workplace, engage in safe behavior, and ensure the safety and health of all parties involved in our business. We will develop the work environment by paying sufficient attention to mental and physical health management.
22. Compliance with Company Rules
In the execution of duties, we will comply with relevant laws and regulations, the Articles of Incorporation, and other company rules which include various our regulations, employment regulations and other regulations related to human resources, operating procedures, and working manuals.
29. Open Working Environment
We will respect each person's individuality and diversity regarding assignment and workplace issues, and always do our best to achieve and maintain a working environment that makes it possible to openly discuss the issues. All management and employees are encouraged not to withhold issues that cannot be resolved in the workplace, and to consult with supervisors and relevant departments in order to strive toward a resolution.
Oji Group Safety and Health Management Rules
The goals of the Oji Group Safety and Health Management Structures are to prevent occupational accidents and enable Group employees, affiliates and business operators entering the Group’s premises temporarily to maintain their good health, clarify responsibilities related tosafety and health in within the Oji Group and stipulate fundamental matters in the Group Safety and Health Management Rules.
Basic Matters
- The Group’s occupational safety and health promotion plan
- Provision of information and guidance regarding safety and health operations to Group companies, management of operations, and reporting of occupational injuries that have occurred
- The Safety and health management operations of worksites in Japan and overseas
Targets and Promotion Plan
Oji Group's Occupational Safety and Health Promotion Plan
Every year, the Oji Group formulates its occupational safety and health promotion plan using insights gained from reflecting on the safety record in the previous year and distributes it to the Group companies.
Using this plan as a starting point, each Group company formulates its own occupational safety and health promotion plan and specific action plans for each company and business site and promotes activities with the goal of eliminating industrial accidents in cooperation with not only Group employees but also contractors and others that enter facilities temporarily.
Basic policies
The Oji Group will promote activities to achieve its target of zero work-related accidents throughout the Group with safety as its absolute top priority.
Slogan
Always follow the main principles for safety and the safety rules and ensure that others follow them to prevent fatal and serious accidents
Key Targets
Zero fatal or serious work-related accidents
Key Measures
As of the end of October 2023, there have been three occupational fatalities (one accident related to forklifts and heavy machinery in Japan, and overseas, one related to a collapse and one to a fire) within the Oji Group, one fatal traffic accident involving a commuting Oji Group employee and two occupational fatalities that are not included in this total (one pinch point accident and one fall accident overseas). Additionally, including the fatalities, there have been 61 accidents accompanied by lost worktime (58 at the same time in the previous year, 69 total that year) and 27 violations of the main principles for safety and workplace safety rules (the same as in the previous year). In the light of these circumstances, we have again posted the slogan, “Always follow the main principles for safety and the safety rules and ensure that others follow them to prevent fatal and serious accidents.” At the same time, we will increase the safety of machinery and equipment with a special focus on measures to prevent collisions with forklifts and heavy machinery, and we will develop initiatives to achieve the goal of zero fatal or serious accidents and reduce the number of accidents accompanied by lost worktime.
- Full compliance with the main principles for safety and related rules
Prepare safety operating procedures containing the rules, prohibited matters and non-stationary operations to regularly provide training to employees with while checking their degree of understanding and learning. Use content related to forklift operations (original content made by Oji, etc.) in virtual reality (VR) hazard experience training. - Improvement of the safety of machinery and equipment (with a special focus on measures to prevent collisions with forklifts and heavy machinery)
Proactively assess risk in a way that enables all employees to participate. Under the direction of the senior management of all of the companies and business sites, managing supervisors shall swiftly and responsibly formulate specific safety measures, and the safety and technical departments shall work together to control progress and improve safety. - Promotion of measures to prevent lower back pain
Do warm-up exercises or stretch before operations. - Management of physical and mental health, and improvement and maintenance of the workplace environment
Maintain and improve health, prevent diseases and detect and treat disease at an early stage by proactively recommending requiring that all employees undergo medical checkups and examinations regularly and that employees with problems undergo follow-up examinations and special health checkups. Additionally, have all employees respond to a job stress questionnaire. Prevent health disorders due to overwork and continue to improve working environments.
Structure
At worksites in Japan and other countries, the head of each worksite who is responsible for the worksite and who has authority over it is its safety and health manager, who is in charge of the overall management of safety and health operations and establishing the safety and health management structure.
In Japan, the heads of mills and other worksites who are responsible for the overall management of the worksites have been appointed the general safety and healthmanager regardless of the scale of the business or industry as prescribed in the Industrial Safety and Health Act.
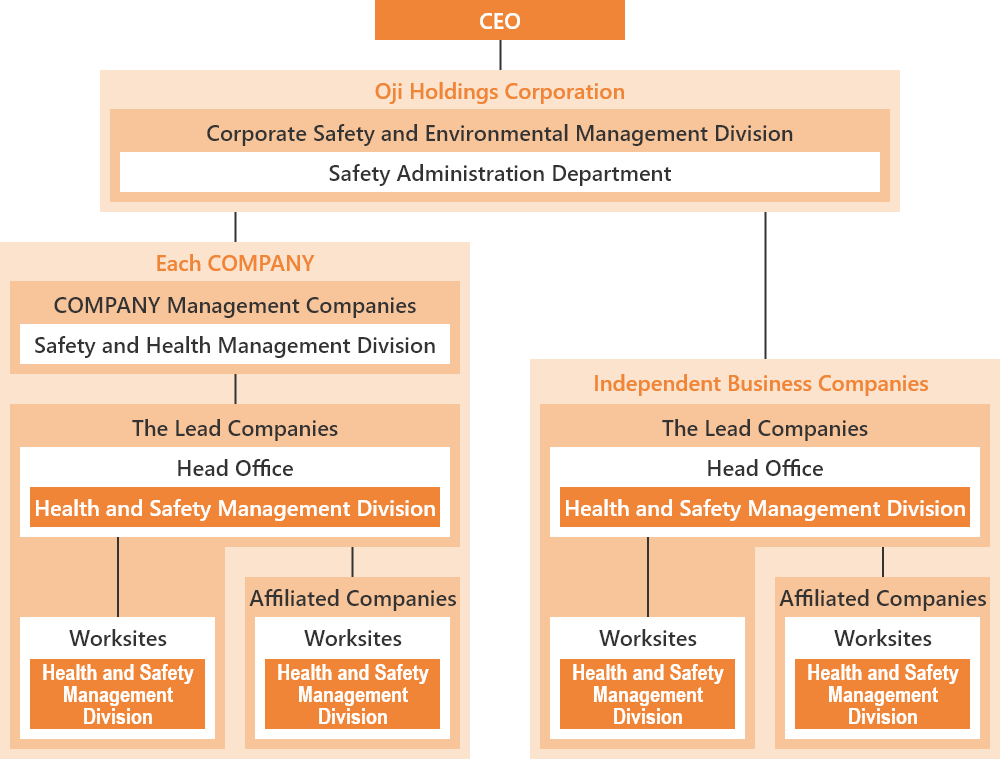
Distribution of Safety and Health Information and Occupational Accident Reports
The Oji Holdings Safety Management Department provides the Group companies with safety and health information, including the Group’s occupational safety and health promotion plan, notices and guidelines.
We have built a structure that ensures that a serious injury, death, or accident that news organizations may potentially report on will be reported to management immediately after it occurs and handled appropriately in accordance with the Group Emergency Response Regulations.
In the event of an occupational injury (resulting in one or more lost work days), a Report On Occurrence of Accident Accompanied by Lost Worktime (Form 1: Preliminary Report) is submitted to the Safety Management Department within three days of the accident. The department confirms basic information about how and why the accident occurred and how to prevent it, and then shares the information with domestic and overseas Group companies and issue instructions to prevent similar accidents throughout the Group.
Further, when an accident has occurred within a Group company in Japan, how and why the accident occurred is studied and analyzed, measures for preventing its recurrence are discussed and implemented at that company and horizontally across the Group, and a Report on Occurrence of Occupational Injury with Temporary Incapacity for Work (Form 2: Detailed Report) is submitted to the Safety Management Department within a month of the accident. The Safety Management Department confirms that effective measures are being implemented to prevent a recurrence of the accident, and then provides information about the measures to Group companies in Japan and other countries, instructing them to reference the information to prevent similar accidents within the Group companies and worksites.
Employee Participation
Occupational safety and health committees, worksite safety and health meetings and worksite discussions
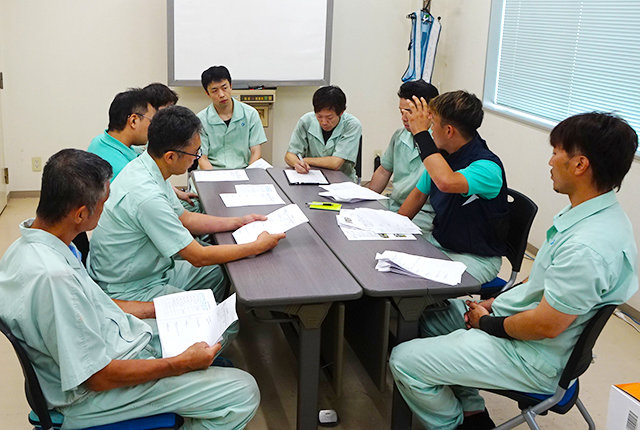
At each domestic worksite, occupational safety and health committees are established in accordance with laws. Guided by these committees, safety and health activities are carried out through cooperation between labor and management. Plans are formulated to prevent occupational accidents and the impairment of health, create comfortable working environments, formulating a plan for maintaining and promoting good health, Issues are also discussed to confirm and improve the initiatives implemented for the plans, and other relevant issues are also covered. We also create opportunities at each worksite to listen to the opinions of many employees, including safety and health meetings and gatherings.
At worksites where the establishment of a safety and health committee is not required by law, we also hold safety and health meetings, gatherings, or similar events on a monthly basis to listen to employees’ opinions regarding safety and health. In addition, because it is essential that all employees work together with cooperative associations (onsite contractors) in their safety and health activities to create an open workplace environment, Oji Group companies and workplaces in Japan attend and jointly hold safety and health meetings with the cooperative associations and hold safety and health meetings that include non-regular employees and temporary employees. Additionally, to limit the spread of COVID-19, meetings are also being held online.
At overseas companies and workplaces, we are working to establish health and safety and committees and health and safety management at each workplace in accordance with the laws and regulations of each country and region. In addition, we have begun holding introduced a safety and health meetings to talk about safety and health, similar events at each worksite to listen to employees’ opinions about safety and health.
Central labor-management committee
The central labor-management committee meets twice a year. The committee includes members of management including the Group CEO and people from Group companies’ labor unions. Information concerning safety is shared at these meetings, including the safety and health activities implemented in line with the Group’s occupational safety and health promotion plan, information about how occupational injuries occurred, initiatives for preventing the occurrence or recurrence of accidents and other information. Oji Group employees discuss the establishment of worksites where they can work safely and with a feeling of security and where their families can feel secure under the basic philosophy, “Safety is our absolute top priority.”
Risk Management
Risk Assessment
We have set "promotion of equipment safety"as a priority measure in the Group's occupational safety and health promotion plan, and have decided to actively conduct risk assessments with the participation of all employees and prevent accidents by implementing specific safety measures that the top management and supervisors of the business units and workplaces are responsible for.
We have focused our risk assessment efforts on the following:
- Safety measures for work near rotating objects
- Measures to prevent crashes and falls when working at a height or on a roof
- Measures to prevent contact with transport vehicles, heavy cargo handling equipment and heavy lifting equipment
- Safety measures for conveyors, balers and pulpers, and measures to prevent workers being exposed to dangerous liquids.
In addition, we have taken specific effective measures, such as intrinsic safety and engineering measures, to prevent the recurrence of accidents or similar accidents.
Risk assessment CY2023
- You can see this table by scrolling horizontally.
Identified methods |
Industrial Materials COMPANY
|
Household and Consumer Products COMPANY
|
Functional Materials COMPANY
|
Forest Resources and Environment Marketing Business COMPANY
|
Printing and Communications Media COMPANY
|
Corporate Management Group
|
Shared Service Companies
|
Oji Holdings
|
Total
|
---|---|---|---|---|---|---|---|---|---|
Company segment | |||||||||
Total | 36,745 | 1,639 | 3,790 | 1,690 | 8,535 | 835 | 3,764 | 1,140 | 58,138 |
Based on work procedure manual | 2,064 | 612 | 2,354 | 261 | 3,774 | 63 | 417 | 575 | 10,120 |
Horizontal deployment of accident cases | 4,698 | 316 | 296 | 459 | 392 | 279 | 353 | 182 | 6,975 |
Safety patrol rules and audit guidance items | 5,803 | 55 | 615 | 322 | 282 | 151 | 1,241 | 127 | 8,596 |
Near miss, incident, etc. | 24,180 | 656 | 525 | 648 | 4,087 | 342 | 1,753 | 256 | 32,447 |
In 2023, as in 2022, we have set "promotion of machinery and equipment safety" as a priority measure in the Group's occupational safety and health promotion plan.
We have decided to use information about the factors in accidents that have occurred* to identify risks, to ensure that top management and supervisors at each company and workplace take responsibility for the planning and management of the progress of specific and prompt safety measures, and to ensure the safety and engineering departments work together to prevent occupational accidents before they occur and prevent their recurrence.
Furthermore, we will use information from accidents, near-misses, safety patrols and the results of audits to proactively conduct risk assessments to prevent the recurrence of accidents or similar accidents.
- * Safety measures for machinery and equipment that involve contact with or work near rotating objects, measures to prevent collisions, falls and objects overturning and measures to prevent contact with cargo handling machinery (transport vehicles, heavy transport equipment and heavy lifting equipment).
Safety audits and safety patrols
The Oji Holdings Safety Management Department and the safety departments of each COMPANY and Lead Company conduct safety audits and safety patrols of the companies and worksites they oversee, including overseas companies and worksites, to improve safety and health management. As a new initiative, we started fixed-point observation in enhanced safety patrols. In addition, we are actively improving the safety of machines and equipment.
Designated System for Special Guidance on Enterprise Safety Management
The Oji Holdings Safety Management Department and the safety departments of each COMPANY and Lead Company established the Designated System for Special Guidance on Enterprise Safety Management. Under this system, companies and worksites where it has been determined that safety management must be improved, such as those where occupational accidents resulting in a serious injury, death or lost worktime have occurred repeatedly within a short period of time are designated worksites needing special guidance on enterprise safety management. Inspections are conducted and guidance is provided, not only regarding measures for preventing the recurrence of accidents but also safety management systems, improvement plans, the status of activities and other matters, to improve the safety management at each designated worksite.
The Oji Holdings Safety Management Department and the safety departments of each internal division/lead company share information and work together to prevent accidents.
On-site accident investigation
The Oji Holdings Safety Management Department and the safety departments of each COMPANY and Lead Company immediately visit worksites where an accident has occurred to confirm how and why the accident occurred, identify countermeasures thoroughly confirm and discuss measures for preventing the recurrence of accidents and daily safety management activities with worksite executives and worksite managers, thereby providing guidance aimed at improving the safety management activities of the worksite as a whole and creating a better work safety climate.
Conducting safety patrols
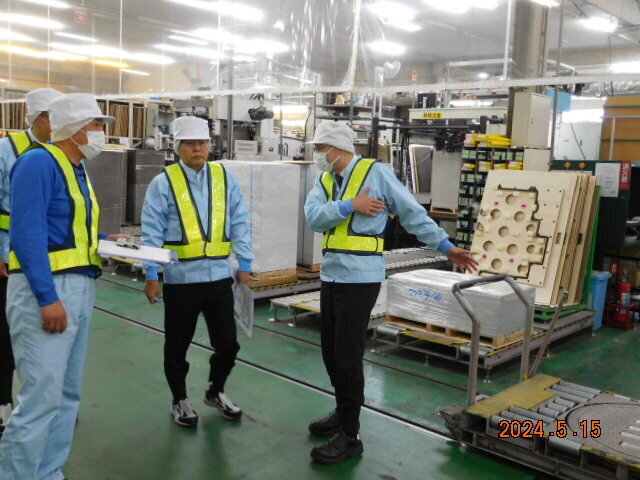
In light of the frequent occurrence of industrial accidents during loading and unloading operations within the Oji Group, the Oji Holdings Group Technology Division and the Oji Holdings Safety Administration Department accompanied Oji Holdings management team members (the Chairman and Executive Vice President) on inspection patrols and began safety-focused inspections, starting with the Oji Container Group, to prevent similar accidents from occurring.
Occupational Safety and Health Management Systems
In Japan, large Group companies including Oji Paper, Oji Materia, Oji F-Tex, and Oji Nepia and small and medium-sized Group companies have established and operate labor safety and health management systems in accordance with the Ministry of Health, Labour and Welfare’s Guidelines on Occupational Safety and Health Management Systems (the OSHMS Guidelines).
Other domestic Group companies also carry out safety and health activities leveraging their the occupational safety and health management systems, including announcing theirthe safety and health policies, ensuring activities reflect the opinions of workers, establishing and implementing the safety and health policies, safety and health targets, and safety and health plan, and daily inspections and improvements.
Overseas Group companies have also established and operate occupational safety and health management systems that are recommended by the organizations overseeing occupational safety and health in each country or region or engage in similar safety and health activities.
Moving forward, we will discuss activities in compliance with the ISO 45001 standard (on occupational health and safety management systems) and the efforts to obtain certification.
Training Programs
The Safety Management Department details job-class-specific and job-specific safety and health training programs that are implemented by the Group companies which use these programs to establish job-class-specific safety and health training programs that are appropriate for the conditions of the individual company. Through these programs, Group companies provide safety and health training (including training provided by external organizations) that is appropriate for each job class and job, in addition to the training prescribed in Industrial Safety and Health Act
Job-class-specific training | Heads of business establishments (heads and deputy heads), managers (managers of departments, offices, and sections, as well as newly-appointed managers), supervisors (leaders of specific operations and works, leaders of small groups and teams, and similar leaders, as well as newly appointed ones), general employees (senior employees, mid-career employees, young employees, fresh graduates, other new employees, and dispatched employees) |
---|---|
Job-specific training | Managers and supervisors, persons who handle hazardous materials, safety and health staff, and personnel assigned to different jobs, personnel whose work contents have been changed, affiliate companies, and business operators who enter the Group’s premises on a temporary basis |
Safety and health education and training
Oji Group companies not only conduct education and training for Group employees in line with the employee’s rank and responsibilities and the Group Safety and Health Education and Training System (draft), but also provide various types of education and guidance to the employees of partner companies stationed on the their premises and construction workers temporarily on their premises.
In addition to these education and training programs, each company and workplace of the Oji Group reads daily safety work procedure manuals, safety rules and detailed regulations, and compliance and prohibition rules, and conducts on-the-job training to ensure that all employees are familiar with safety rules. Recently, we have installed hazard simulation equipment and have had employees participate in courses provided by external institutions. In addition, we have developed Group-wide hazard simulation training using VR technology, which enables employees to safely and effectively experience simulated collisions, crashes, falls, electric shocks, contact with harmful objects, flying and falling objects and collapses which are difficult to simulate. This is designed to improve employees’ sensitivity to danger and safety awareness through firsthand experience with hazards.
Hands-on risk training using hazard simulation VR devices
Since 2020, we have gradually begun conducting hands-on risk training sessions using VR at workplaces in Japan and overseas. Many participants have talked about the highly immersive VR videos. One said, “In the disaster experience video, I reflexively flinched and tried to run. The video enabled me to experience accidents in a way that is not otherwise possible. I realized how scary accidents are and my understanding of the importance of following rules has been renewed.” Having produced original, experience-based content, including content reflecting case studies of accidents that have occurred within the Oji Group, we exercised ingenuity using the 14 VR scenarios so that students can learn not only in environments that are close to their day-to-day operations but also from fresh perspectives.
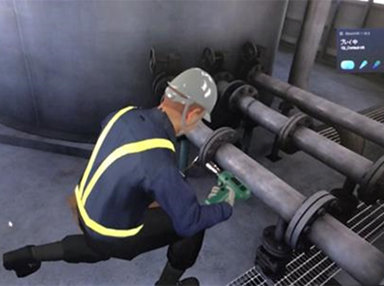
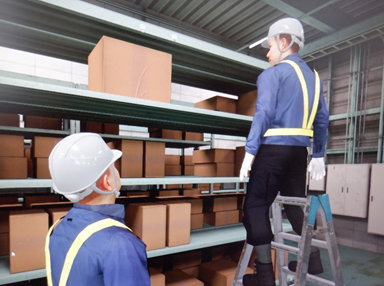
Original content (falling from stepladders, contact with harmful objects)
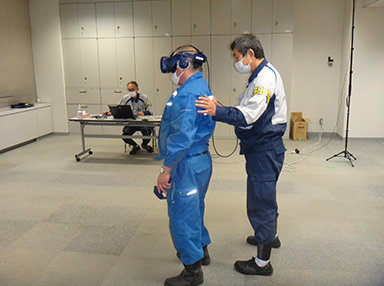
Safety Activities at Oji Group Companies
Forklift competition
Oji Group companies in China have been holding Forklift Safety Workshops and Skills Competitions since 2014. The events provide knowledge regarding forklifts and improve operating skills with the goal of achieving zero forklift accidents. During the forklift safety workshops, participants analyze the causes of forklift accidents, watch safety videos and actively participate in question-and-answer sessions, enhancing their awareness of safety.
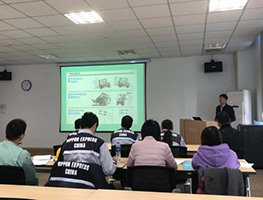
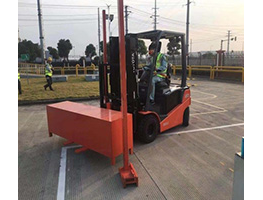
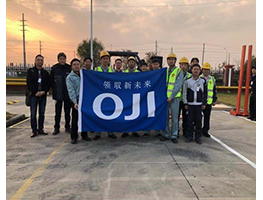
Hazard prediction training (KYT)
We are engaged in hazard prediction training (KYT) using KY sheets and case studies of accidents that have occurred within the Oji Group to increase every employee’s sensitivity to danger, detect hidden risk factors in various conditions and situations and study various measures for improving people’s sensitivity to danger and preventing accidents.
(Group companies in Southeast Asia under the control of Oji Asia Packaging of the Industrial Materials COMPANY: since 2020.
Group companies in China under the joint control of the individual COMPANIES and Oji Paper Management (Shanghai) Co.: since 2021.)
Participants commented on the training, saying, “There are seeds of danger lurking in things that we normally do without thinking,” “There are seeds of danger that I am not aware of,” and “I want to make use of this information in my work in the future.”
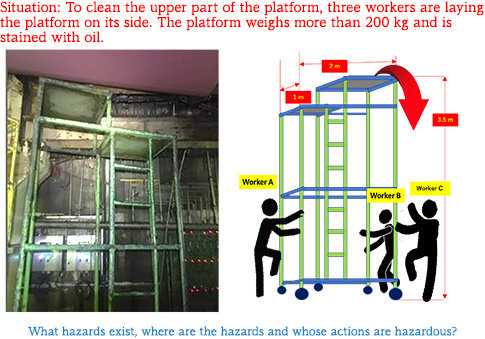
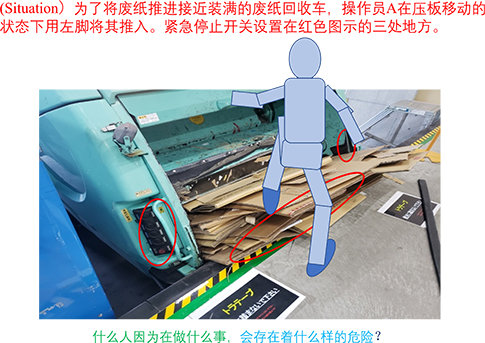
Hazard prediction training (KYT)
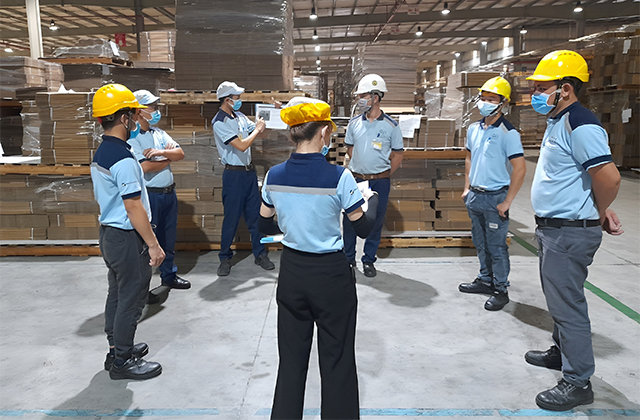
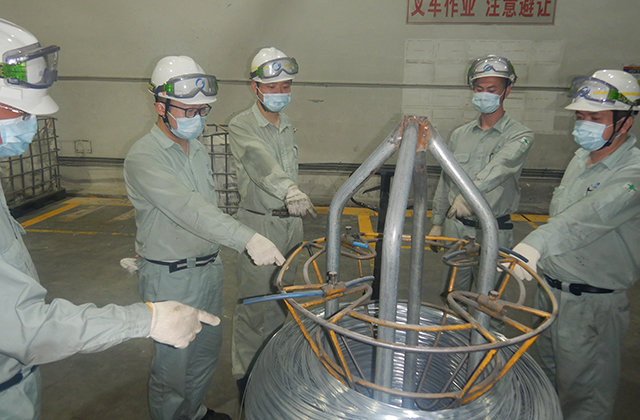
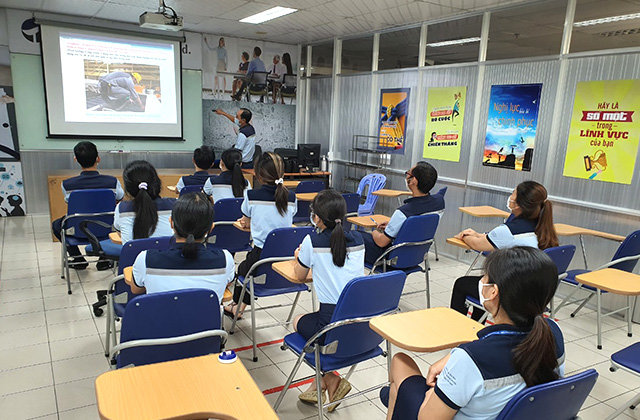
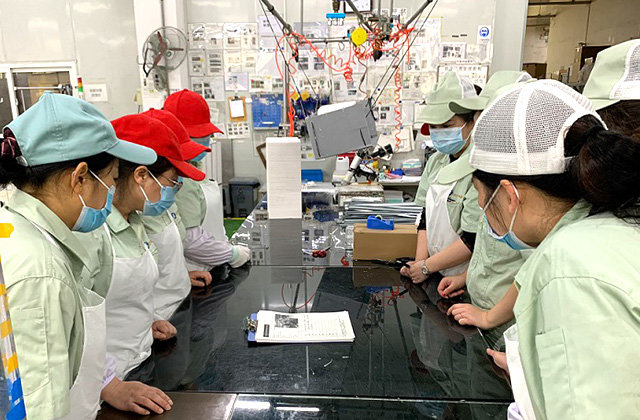
Safety Award
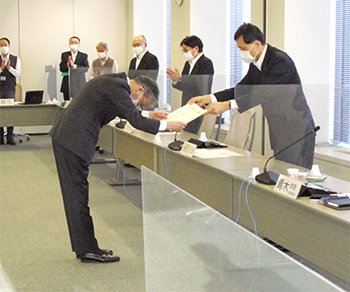
The Group CEO Safety Award is granted to all of the Oji Group domestic and overseas worksites that meet certain criteria determined according to the scale of the business (number of employees), including total work time without an occupational accident resulting in temporary incapacity for work and the number of consecutive years with no occupational accidents. The award is granted to worksites with an outstanding record of no accidents while working together with the employees of those worksites and the affiliates of Group companies with the goal of improving the safety and health of the Oji Group and eliminating occupational accidents.
In addition, the Oji Holdings Safety Management Department conducts interviews and on-site inspections at workplaces that have been presented the Group CEO Safety Award. The department provides Group companies with information about these worksites as good examples of safety activities as a measure for increasing the safety awareness of the Group as a whole and improving its safety climate. We have also introduced the COMPANY President Safety Award and the President Safety Award withing each Group company, and the Worksite Head Award as safety award programs commending companies, worksites and divisions within each COMPANY and Group company with excellent safety.
Data
The Oji Group aims to eliminate occupational injuries by implementing initiatives to achieve zero fatal and serious work-related accidents guided by the basic philosophy, “Safety is our absolute top priority.”
Number of accidents resulting in lost worktime
The numbers of industrial accidents* that occurred throughout the entire Group in the most recent years (including accidents at non-consolidated affiliates) are as follows:
2021
There were 71 occupational accidents (45 in Japan and 26 overseas), but no fatal or serious accidents.
2022
In 2022, two fatal accidents occurred in Japan and one overseas. There were 66 lost time accidents (39 in Japan and 27 overseas).
2023
In 2023, there was one fatal accident in Japan and two overseas. There were 65 lost time accidents (41 in Japan and 24 overseas), of which 34, approximately half of them, were caused by violations of safety rules. Therefore, as a safety measure in the following year, 2024, we are striving to eliminate occupational accidents by continuing to emphasize Complete Adherence to the Main Principles of Safety and Safety Rules as we did in 2023.
- *Industrial accidents:
・For employees and cooperative companies: Fatal accidents and accidents resulting in at least one day of lost worktime
・ For contractors entering facilities temporarily: Fatal accidents
The number of accidents resulting in lost worktime above excludes accidents at overseas Group companies that are determined to be at the level of accidents accompanied by injuries without lost worktime in Japan (2020: 24 accidents, 2021: 17 accidents, 2022: 33 accidents, 2023: 52 accidents) to facilitate comparisons between safety in Japan and overseas.
Lost time injury frequency rate
The lost time injury frequency rate for Oji Group domestic workplaces has been trending upward since 2019, but it turned downward in 2023, dropping to 0.80.
This is low compared to the figures for Japan’s manufacturing industry as a whole and for the pulp, paper and processed paper manufacturing industry (according to data from the Ministry of Health, Labour, and Welfare's Survey of Occupational Accident Trends).
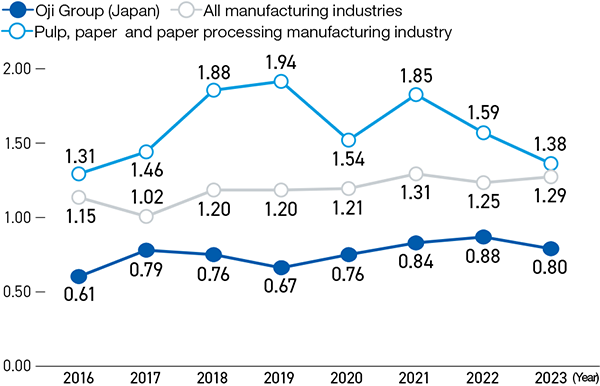